Optimizing Overhead Conveyor Systems for the Garment Industry
The garment industry demands efficient logistics and streamlined operations to manage the high volume of clothing production, sorting, and distribution. Overhead conveyor systems have emerged as a key solution, revolutionizing the way garments are handled. In this blog, we'll explore the types of garment handling conveyor systems, their role in improving logistics efficiency, installation and maintenance tips, and common issues with their solutions. Let's dive into the world of garment conveyor systems and how they are transforming the garment industry.
Types of Garment Conveyor Systems
Different types of garment conveyor systems cater to the unique needs of the garment industry. Here are the most common ones:
1. Closed-Track Garment Conveyor Systems:
● Ideal for high-capacity operations, these systems ensure garments remain clean and organized.
● Widely used in dry cleaners, uniform services, and large warehouses.
2. Overhead Monorail Systems:
● Perfect for transporting garments over long distances within a facility.
● These systems save space and are highly customizable.
3. Garment Conveyor Systems with Sorting Capabilities:
● Designed for automated sorting and efficient handling.
● Common in e-commerce fulfillment centers and large-scale garment manufacturers.
4. Retail Display Clothes Conveyor Systems:
● Allow dynamic rotation of garment items for display, ideal for retail environments.
● Combine aesthetic appeal with functional garment handling.
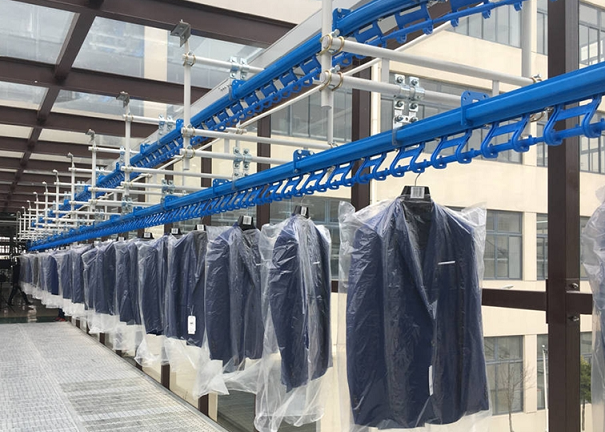
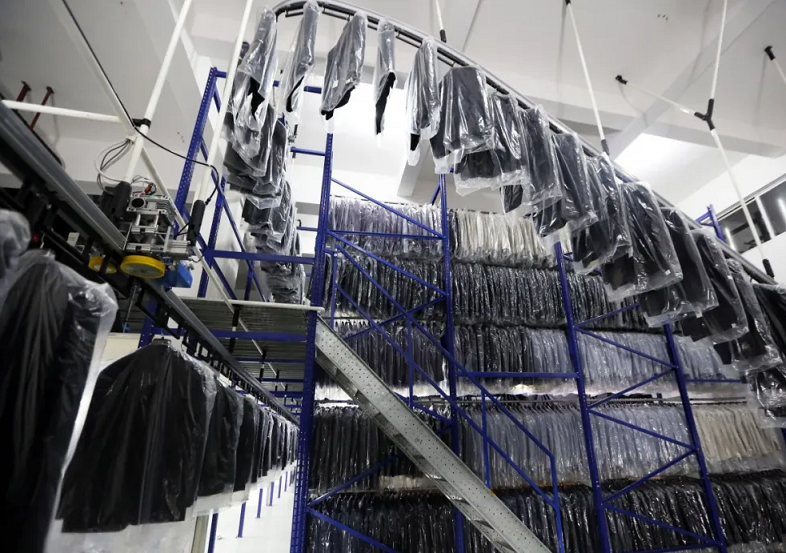
Improving Logistics Efficiency
Efficient logistics are crucial for the success of the garment industry. Here's how garment conveyor systems enhance operations:
1. Automated Sorting and Distribution:
● Automated systems reduce manual handling and errors, ensuring garments reach their destinations faster.
2. Space Optimization:
● Overhead systems free up floor space, allowing for better organization and increased storage capacity.
3. Reduced Labor Costs:
● By automating processes like garment sorting and transportation, businesses can reduce reliance on manual labor.
4. Improved Workflow:
● Streamlined conveyor systems ensure smooth transitions between production, packaging, and distribution stages.
Installation and Maintenance Tips
Proper installation and regular maintenance are critical for the longevity and efficiency of garment conveyor systems. Follow these best practices:
1. Professional Installation:
● Hire experts for accurate system setup to avoid misalignment and operational inefficiencies.
2. Routine Maintenance Checks:
● Regularly inspect the system for wear and tear, particularly chains, bearings, and rollers.
3. Lubrication and Cleaning:
● Keep moving parts well-lubricated and clean to prevent breakdowns.
4. Employee Training:
● Ensure staff are trained in system operation and basic troubleshooting techniques.
Common Issues and Solutions
Even the best garment conveyor systems can encounter issues. Here are some common problems and their solutions:
1. Chain Misalignment:
● Issue: Chains may become misaligned over time, causing uneven movement.
● Solution: Regularly inspect and recalibrate chains during maintenance.
2. Excessive Noise:
● Issue: Noise may indicate insufficient lubrication or worn-out components.
● Solution: Apply lubricant promptly and replace damaged parts.
3. Overloading:
● Issue: Heavy loads can strain the conveyor system and lead to breakdowns.
● Solution: Adhere to the system's load capacity and distribute weight evenly.
4. Electrical Failures:
● Issue: Power issues may disrupt the operation of the conveyor system.
● Solution: Check wiring and connections and ensure proper grounding.
Case Studies:
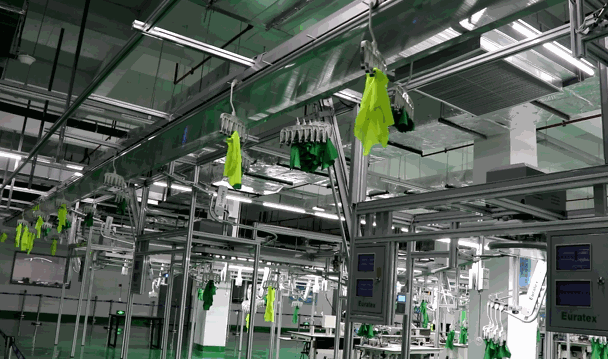
Optimizing Garment Handling for a Major Retailer
A global retail brand implemented a garment conveyor system to optimize its warehouse operations. The closed-track conveyor system enabled automated sorting for thousands of garments. Results included:
● A 40% reduction in order processing time.
● A 30% increase in floor space utilization.
● A 25% reduction in labor costs due to minimized manual handling.
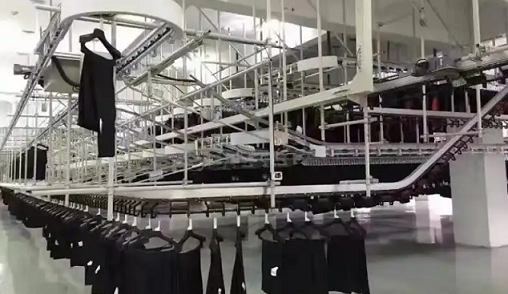
Enhancing Efficiency in a Uniform Service Company
A leading uniform service provider adopted a clothes conveyor system to handle large volumes of garments efficiently. The system was equipped with automated sorting and tagging capabilities, enabling seamless tracking and organization. Outcomes included:
● Faster turnaround times for cleaning and delivery.
● Improved customer satisfaction with accurate order handling.
● Significant reduction in manual sorting errors.
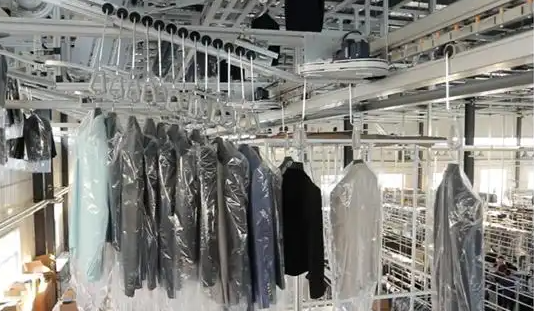
Retail Display Transformation
A high-end fashion retailer installed a clothing conveyor system in its flagship store to enhance visual merchandising. The rotating conveyor showcased garments dynamically, attracting customer attention and increasing sales. Benefits included:
● A 20% increase in customer engagement.
● Enhanced brand image through innovative display solutions.
● Streamlined inventory management for display items.
Garment conveyor systems are an indispensable part of the modern garment industry, offering solutions for efficient handling, space optimization, and cost savings. By understanding the types of systems available, ensuring proper installation and maintenance, and addressing common issues, businesses can unlock the full potential of these innovative systems.
Ready to revolutionize your garment logistics? Explore the limitless possibilities of garment conveyor systems, clothes conveyor systems, and clothing conveyors, and elevate your operations to a new level.