From Raw Material to Finished Product: Conveyor Manufacturing Process Explained
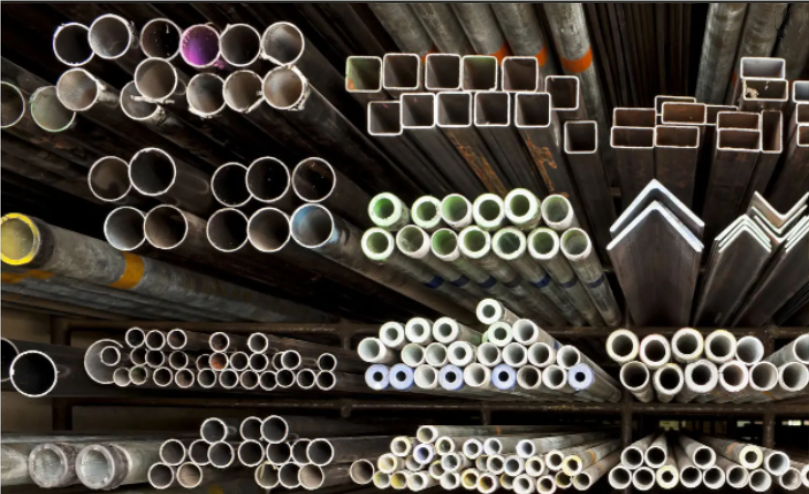
Conveyor systems are the backbone of modern manufacturing and logistics operations. They efficiently transport goods and materials from one place to another, ensuring seamless production and distribution processes. But have you ever wondered how these essential pieces of equipment are made?
In this blog, we will delve into the fascinating world of conveyor manufacturing, exploring how raw materials are transformed into the robust conveyor systems we rely on every day.
The Raw Material Selection
The journey from raw material to finished product begins with the selection of high-quality materials. The choice of materials depends on the specific requirements of the conveyor system, such as load capacity, durability, and environmental conditions.
● Steel: Steel is a popular choice for conveyor frames and components due to its strength and durability. It can withstand heavy loads and harsh operating conditions.
● Aluminum: Aluminum is often used for lighter conveyor systems or in applications where weight reduction is important. It is also resistant to corrosion, making it suitable for use in wet or humid environments.
● Rubber and Plastics: The conveyor belt is often made from rubber or various types of plastic, depending on the application. These materials provide flexibility, durability, and resistance to wear and tear.
The Manufacturing Process
● Cutting and Shaping
Once the raw materials are selected, the manufacturing process begins with cutting and shaping. Steel or aluminum sheets are cut into the required sizes and shapes using precision cutting tools such as laser cutters or plasma cutters. These tools ensure accuracy and consistency, which are crucial for the proper assembly of the conveyor components.
● Welding and Assembly
After cutting, the components are welded together to form the structural frame of the conveyor. Skilled welders use techniques such as MIG (Metal Inert Gas) welding to join the metal pieces. The welding process must be precise to ensure the strength and integrity of the frame. Once the frame is assembled, other components such as rollers, pulleys, and supports are attached using bolts and fasteners.
● Machining and Finishing
Some components, such as rollers and pulleys, require additional machining to achieve the required precision and smoothness. These components are often turned on lathes or machined on milling machines to ensure they fit perfectly with the conveyor belt or chain. After machining, the components are finished with a protective coating such as paint or powder coating to prevent corrosion and enhance durability.
● Conveyor Belt or Chain Installation
The conveyor belt or chain is then installed onto the frame. For belt conveyors, the belt is carefully wrapped around the rollers and pulleys, ensuring proper tension and alignment. In the case of a case conveyor chain, the chain is assembled and connected to the drive system. The installation process requires precision to ensure the belt or chain runs smoothly without slipping or misaligning.
● Testing and Quality Control
Before the conveyor system is shipped to the customer, it undergoes rigorous testing and quality control procedures. The conveyor is tested for load capacity, speed control, and overall performance. Any issues or defects are identified and corrected to ensure the system meets the highest standards of quality and reliability.
Customization and Innovation
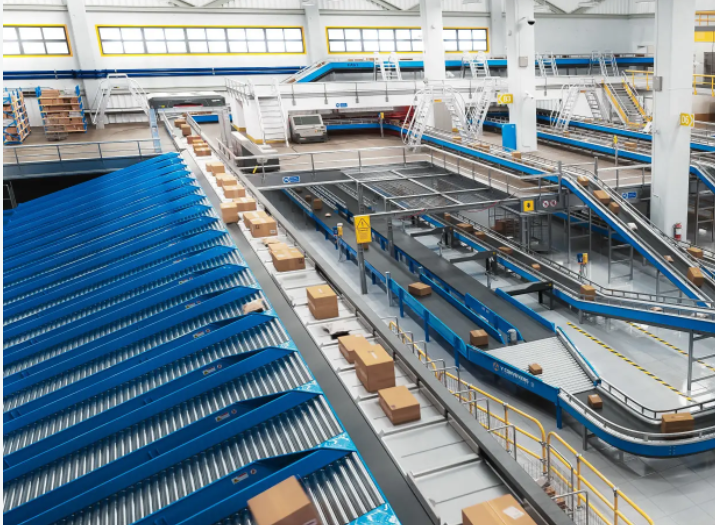
One of the key advantages of conveyor systems is their ability to be customized to meet specific customer requirements. Manufacturers can tailor the design, size, and components of the conveyor to fit the unique needs of each application. This customization ensures that the conveyor system is optimized for efficiency and productivity.
In addition to customization, continuous innovation in conveyor manufacturing is driving improvements in efficiency, durability, and sustainability. New materials, advanced manufacturing techniques, and smart technologies such as sensors and automation are being integrated into conveyor systems to enhance their performance and capabilities.
The manufacturing process of conveyor systems is a complex and fascinating journey from raw materials to finished products. It involves careful selection of materials, precise cutting and shaping, skilled welding and assembly, and rigorous testing to ensure the highest quality. Understanding this process helps us appreciate the engineering and craftsmanship that goes into creating these essential pieces of equipment. Whether it's a simple belt conveyor or a sophisticated case conveyor chain system, each conveyor is designed and built to meet the demands of modern industry and keep the world's goods moving smoothly.